Full-scale Launch of Forklift Operation Analysis System
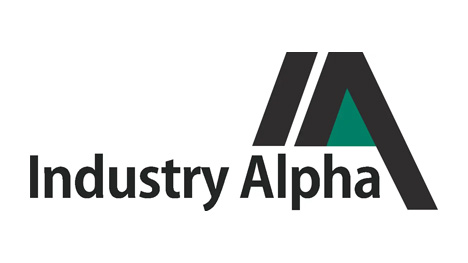
~ Promoting Automation at Logistics Sites through Visualization of Forklift Operation Status ~
Overview
Industry Alpha Co., Ltd. (development base: Nagoya City, Aichi Prefecture; CEO: Takumi Watanabe), which operates smart factory and warehouse business with the mission of “designing and realizing smart factories and smart warehouses,” including the development and introduction of low-floor AMRs (Autonomous Mobile Robots), has commenced the full-scale deployment of its independently developed forklift operation analysis system. This initiative aims to improve productivity at logistics sites by visualizing forklift operations in logistics centers and factories.
Industry Challenges and Automation Policy
The manufacturing and logistics industries are facing labor shortages due to factors such as population decline and aging, increasing the need for automation. Among these, the shortage of forklift operators is becoming serious, and each site is being forced to respond to how to operate tasks traditionally performed by forklifts going forward.
As solutions to the forklift operator shortage, the following three approaches are considered:
- Full Automation by AGF (Automated Guided Forklift)
This automation method replaces currently operated manned forklifts by introducing autonomous forklifts that automate everything from loading/unloading to transport and loading operations seamlessly.
- Semi-automation combining AMRs (Autonomous Mobile Robots) and manned forklifts
In this method, forklift operators continue to handle loading/unloading tasks which are difficult to automate, while transport tasks are handled by transport robots such as AMRs. For example, a forklift unloads pallets from trucks, and an AMR receives and automatically transports them to storage locations.
- Work efficiency improvement by operational optimization of existing forklifts
This method improves productivity by optimizing operations based on work analysis while utilizing existing equipment. Examples include reviewing forklift operator shifts and optimizing transport routes.
“1. Full Automation by AGF (Automated Guided Forklift)” is technically demanding and has not progressed much in introduction due to constraints such as takt time required at logistics sites. Our company contributes to realizing “2. Semi-automation combining AMRs” and “3. Operational optimization of existing forklifts” through this forklift operation analysis system.
About the Forklift Operation Analysis Box
There are several challenges in semi-automation with AMRs and operational improvement of existing forklifts. In semi-automation, “calculating the required number of AMRs” and “predicting cost-effectiveness of automation” are important considerations, while in operational improvement, “understanding forklift operation status” is a critical item.
Therefore, our company has developed an operation analysis box that can be externally installed on existing forklifts to acquire forklift location information and visualize data such as “what percentage of operating time each forklift spends on loading/unloading and what percentage is spent traveling empty” and “which travel routes are taken.” This contributes to semi-automation and efficiency improvement of existing forklifts.
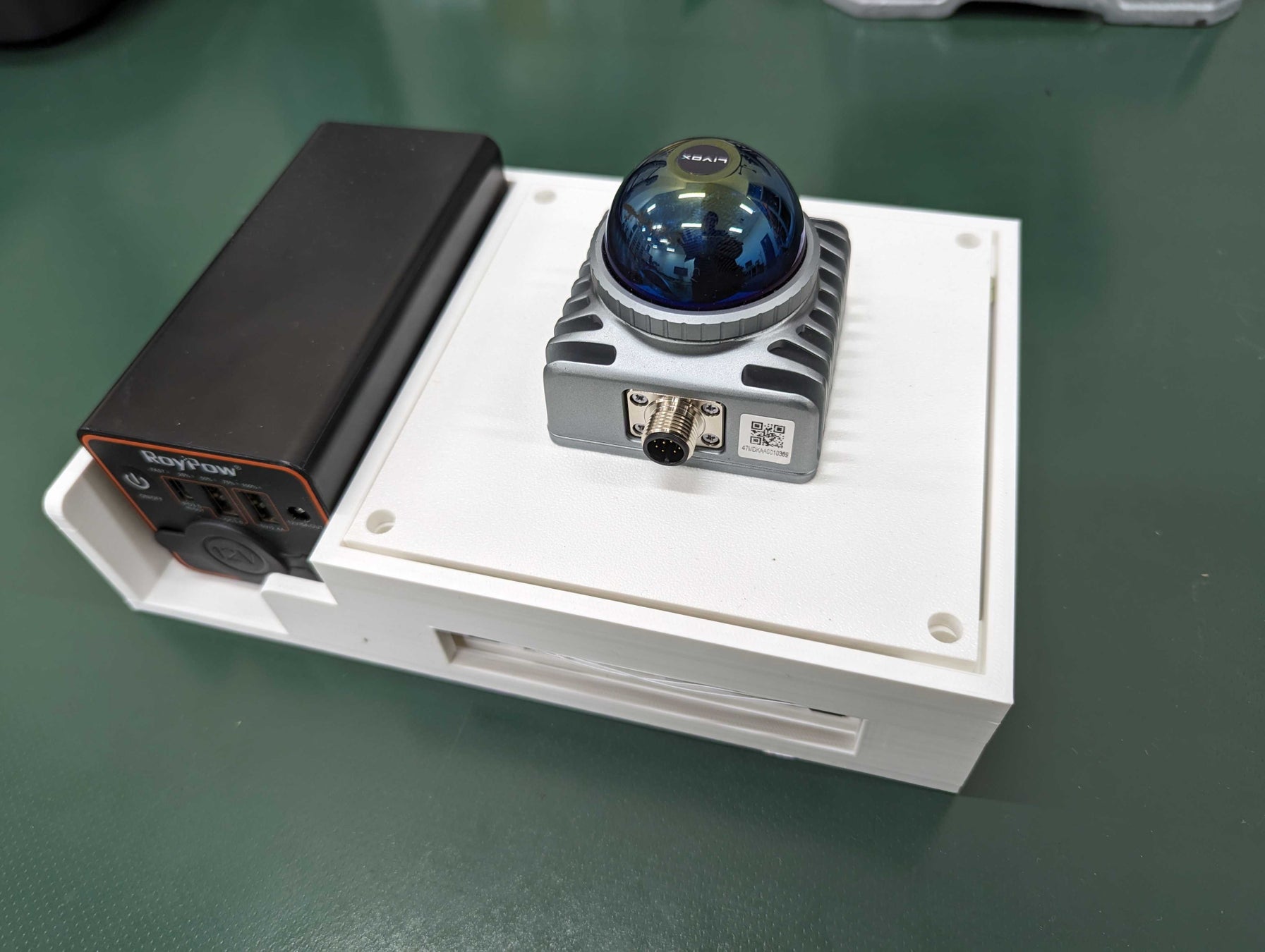
Our measurement box is equipped with a LiDAR sensor (infrared sensor). By analyzing forklift location information using the LiDAR sensor, the following data can be obtained.
Analyzable Data
Differences in work efficiency among forklift operators
(To what extent there are differences in transport distance and work efficiency among forklift operators)
Breakdown of each forklift’s tasks
(What percentage of operating time is spent on unloading/loading work, horizontal transport, and empty travel)
Breakdown of travel speed ranges
(What percentage of operating time is spent at high speed, low speed, and ultra-low speed)
Heat map
(Which areas within the site have frequent cargo removal and where forklifts are concentrated)
Features
- Ease of Installation
Conventional forklift operation analysis required installing beacons on ceilings and large-scale construction inside warehouses and factories. In sites with high ceilings, scaffolding installation was necessary, resulting in construction costs ranging from hundreds of thousands to millions of yen. Additionally, work in the relevant area had to be stopped during the construction period, impacting site operations.
However, with this solution, there is no need to install equipment on the environment side, and by selecting inexpensive infrared sensors, low cost and easy installation are realized.
- Operation Optimization through Visualization
Through analysis, idle time and the number of forklifts needed by time of day become clear.
As a result, the number of forklifts and forklift operator shifts can be optimized, improving operation of existing forklifts.
- Automation Effect Calculation Possible
Based on visualized data, it becomes clear “how many AMRs need to be introduced to achieve what level of labor cost reduction,” enabling formulation of future warehouse and factory automation policies.
- Realization of Cooperative Control between AMRs and Forklifts
In addition to effect measurement, this solution can be used for cooperative control between AMRs and forklifts. By extending this solution and checking forklift positions in real time, safety management when AMRs and forklifts approach each other becomes possible. For example, confirming whether forklifts are staying in the area AMRs are heading to and stopping AMRs before entering if forklifts are present in that area. Furthermore, cooperation such as automatically directing AMRs to locations where forklifts have loaded or unloaded cargo can also be implemented.
Future Outlook
This solution enables visualization of forklift operation status, which has been difficult to quantify until now. Leveraging the ease of installation that requires no environmental construction and simply attaching the box to existing forklifts, we will promote adoption in various sites.
The collected data will first be used to improve operational efficiency at each site. Furthermore, based on forklift operation analysis data, we aim to realize efficient semi-automation combining AMRs and manned forklifts. Loading and unloading tasks, which are difficult to automate, will continue to be handled by manned forklifts, while AMRs will perform tasks such as horizontal transport of pallets, achieving efficient logistics operations.
In the future, by utilizing the vast data collected from forklifts, we will contribute to realizing next-generation smart factories where all equipment and systems within factories are interconnected.
Please refer to the following for examples of actual site applications.
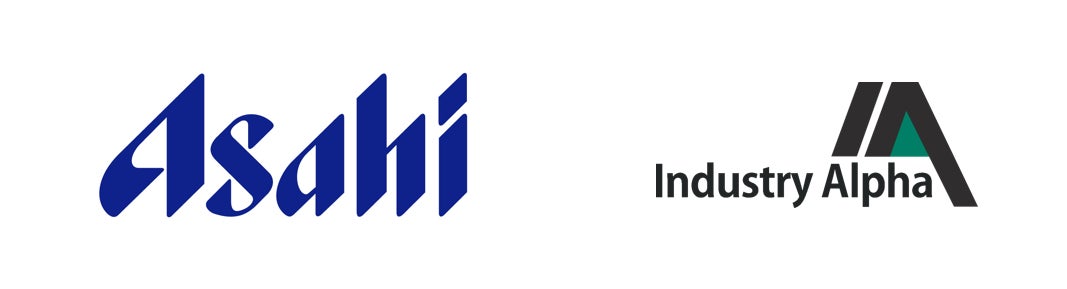