【物流DXの最先端】Industry Alphaと大洋紙業が物流倉庫における自動化に関する取り組みを開始
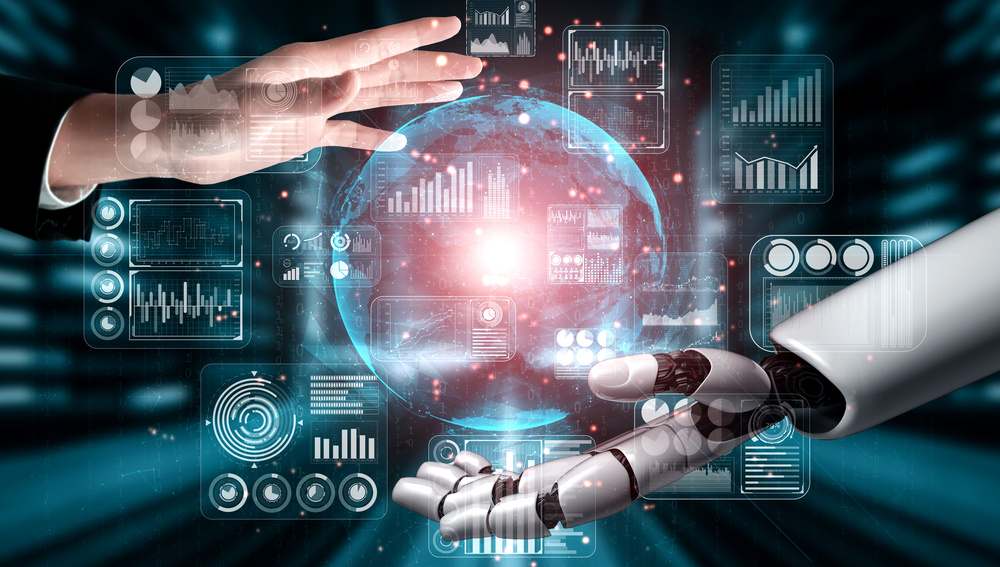
背景
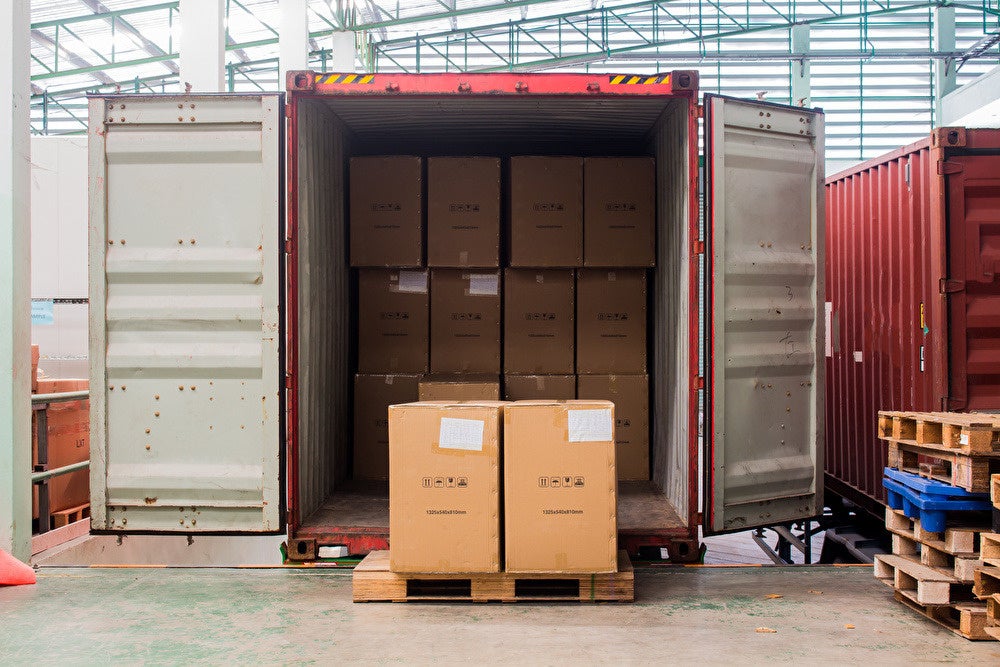
昨今の⽇本の製造・物流業界の要である倉庫は、EC市場の拡⼤や労働⼈⼝の減少に伴い、更なる効率化が求められています。実際に、倉庫の自動化によって⼤幅な⼈件費の削減や⽣産効率の最⼤化が⾒込めます。
倉庫の自動化には、ロボットやAIを導入するだけではなく、後の拡張性を考慮して倉庫全体の設計をすることが必要です。
これまで、倉庫の建設段階から物流ラインを描く自動倉庫は、一部の企業のみが導入を実現しているものの、巨額な設備投資が必要なため、多くの企業は既存の倉庫の自動化を求められていました。
しかし、既存の倉庫を自動化していく中で、システムが合わない、市販の製品では対応できないなど自動化を断念するケースが頻発しています。
そのため、既存の倉庫を部分的に自動化してくことで倉庫の最適な運用を可能にするソリューションが求められていました。
自動化に関する取り組み内容

今回、Industry Alphaと大洋紙業は物流倉庫を間借りし、倉庫内物流ラインの自動化に関する取り組みを開始いたしました。
この取り組みでは、巨額な資金投資を必要とする立体倉庫やセンターの建築を必要とせずとも、物流ラインにおける最適なマテリアルハンドリング機器の組み合わせを設計することで従来の倉庫では人が担っていた作業をスマート化し、物流ラインの自動化を実現いたします。
当社は、省人化・効率化のプロフェッショナルとして、既存倉庫の自動化をサポートいたします。
従来の倉庫における課題
従来の倉庫における物流ラインではピッキングと搬送に多くの従業員の方の労力がかかっていました。
ピッキングは、倉庫運用コストの約50%を占めると言われています。作業員の方がリストを見ながら商品を探すことで倉庫内を何度も移動しており、ピッキング作業の改善は生産性向上を図る上で非常に重要な課題となっています。
また、搬送も人がハンドリフトで荷物を運搬する現場が多く、荷物をハンドリフトから落としてしまいトラブルになるケースもあります。
さらに、多くの梱包現場では、ラベルの貼り付けや段ボールの組み立てを作業員の方が担当しており
下記のような課題を抱えていました。
- 人によってスピードに差が出てしまう
- 商品の入れ間違いや同梱物の入れ忘れが発生している
- 作業員の高齢化で梱包手順の教育コスト増加
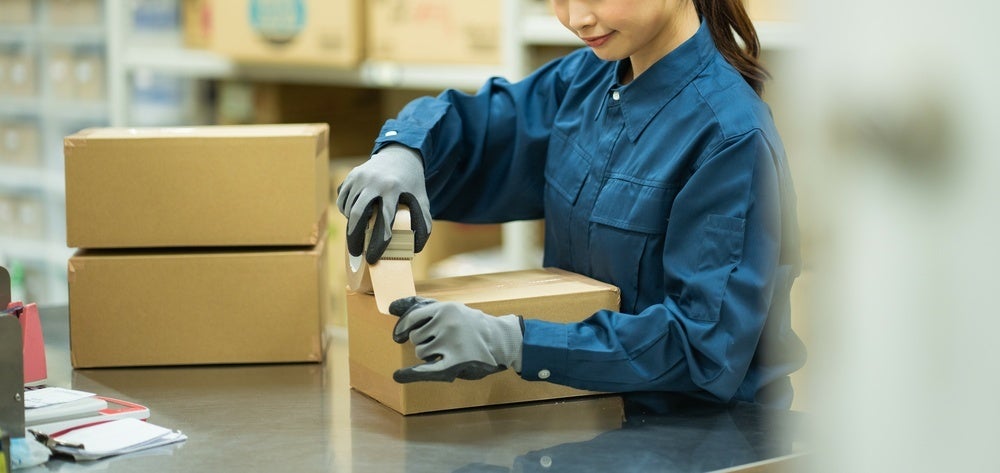
Industry Alphaが搬送・ピッキングの課題を、大洋紙業が梱包の課題に取り組みました。
両社はこれらの課題に対し、業務の全体オペレーションが最適になるように解決案を設計いたしました。
Industry Alphaの課題解決
当社は従来の倉庫の課題であったピッキング、搬送をそれぞれの工程とシナジーを生むようにDX化することで、既存の倉庫をスマート倉庫へと変革し、大幅な人件費の削減と生産性の向上を可能にする製造物流ラインを実現いたします。
当社はまず、ピッキングと搬送を同時に行えるピッキングアシストAGVを開発いたしました。ピッキングの際に荷物を載せる棚を、車体上部に搭載した最先端AGVとなっております。作業員の方がピッキングを行い、AGVに荷物を置くことでAGVが自動的に搬送を完了いたします。こちらのAGVによって、ピッキングエリアの省人化が可能となります。
また、WMSのピッキングリストを、経路を考慮した最適な順番で並べ替える、順序最適化モジュールとピッキングアシストAGVを組み合わせることで、複数台のAGVの最適経路を自動で算出するシステムを開発いたしました。
これにより、人が行う作業はAGVのいる場所に行き、ピッキング及び検品作業を行うのみとなります。
さらに、自動ラベル貼り付け機や自動製函機を導入することで、入庫から出庫までの一連の流れの中で、人が行う作業を積み下ろし、ピッキング、積み込みのみに大幅に削減するスマート倉庫の実現が可能となっております。
具体的な作業効率のベンチマークは下記の通りです。
まずはこれらのベンチマークを実現し、今後は様々な工夫を施して、ピッキング1件あたりのさらなる短縮を目指します。
Before
・人のみのピッキング時間:50秒/ピック
・人のみの梱包時間:60秒/件
After
・人+ロボットのピッキング時間:30秒/ピック
・人+自動ライン時間:30秒/件
今後の展望
当社は今回、大規模な立体倉庫を導入せずとも、既存の倉庫のスマート化によって究極的な省人化・物流ラインの自動化を実現いたします。スマート化によって庫内業務のデータ蓄積が可能になったことで、出荷頻度や出庫頻度のデータ分析から入庫、入荷の最適化も期待できます。
また、ロボットアームとAMRを組み合わせることで、今回の取り組みにて人が行っている、積み下ろし、ピッキング、積み込みを自動化し、無人倉庫を実現いたします。
さらにロケーション管理を行うことで、出荷時にピッキングの効率がよくなる配置を算出するなど、さらなる省人化・スマート化を実現して参ります。