[Industry Alpha x Aichi Prefecture] Startup aiming to reduce labor in factories and warehouses selected for “New Aichi Creative Research and Development Subsidy”
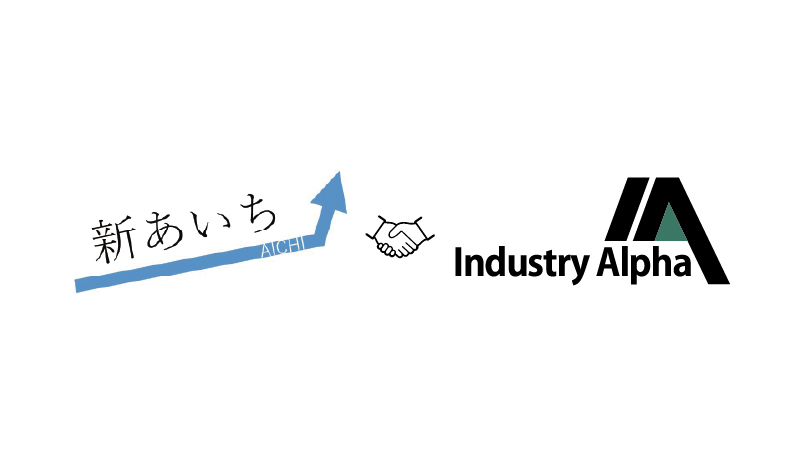
Industry Alpha utilizes subsidies to improve the quality of its in-house developed AMR software, contributing to strengthening the competitiveness of Aichi Prefecture’s core manufacturing industry
overview
Industry Alpha Inc. (Headquarters: Itabashi-ku, Tokyo; R&D base: Nagoya City, Aichi Prefecture; Representative: Takumi Watanabe), which operates a business to make factories and warehouses smarter, including developing and introducing low-floor AMRs (Autonomous Mobile Robots), has been selected for Aichi Prefecture’s “New Aichi Creative Research and Development Subsidy” for fiscal 2024. This subsidy has been in operation since 2012 as a measure against the hollowing out of industry, and this year 161 companies applied, with 61 being selected, from large and small companies in fields expected to grow in the future (next-generation automobiles, aerospace, environment and new energy, health and longevity, information and communications, robotics, etc.).
What is the “New Aichi Creative Research and Development Subsidy”?
In response to the worsening hollowing out of industry, Aichi Prefecture has been operating a groundbreaking subsidy system using the “Deindustrial Hollowing Out Countermeasure Tax Reduction Fund” since fiscal 2012. Deindustrial hollowing out refers to the phenomenon in which domestic industrial base is weakened as companies, mainly in the manufacturing industry, relocate their production bases overseas.
This problem is not limited to companies simply moving overseas, but is a serious issue that shakes the foundations of Japanese manufacturing, such as a decrease in domestic employment and the outflow of technological capabilities, and the impact is becoming more serious when combined with the population decline problem facing Japan.
Our company will not only develop and introduce AMR and its control system, but also design smart factories and warehouses in a one-stop manner, realize factory and warehouse operation with fewer people, and contribute to maintaining the competitiveness of Japan’s manufacturing and logistics industries.
The theme of Industry Alpha in the “New Aichi Creative Research and Development Subsidy”
About this initiative
With this grant, we will proceed with updating the software for our proprietary AMR. We aim to improve the quality of the autonomous driving algorithm that enables AMR to estimate its own position and generate a route towards the goal.
What is AMR?
AMR has been attracting attention in recent years as a means of automating transportation in the logistics and manufacturing industries. The method of transporting luggage varies depending on the machine, including a lift-up type that crawls under a cart and lifts it up, and a towing type that hooks a cart and runs. Conventional AGVs (automated guided vehicles) used for automatic transportation mainly use magnetic tapes or QR codes installed on the ground and run on them.
These have difficulty responding flexibly to changes in the environment, and it was necessary to replace the magnetic tapes or QR codes every time the layout was changed. On the other hand, AMR uses LiDAR sensors (sensors that emit infrared rays) to run, so there is no need to install guides on the floor, etc. Therefore, it is easy to introduce and change the layout, and it is characterized by its flexible movement in cooperation with workers.
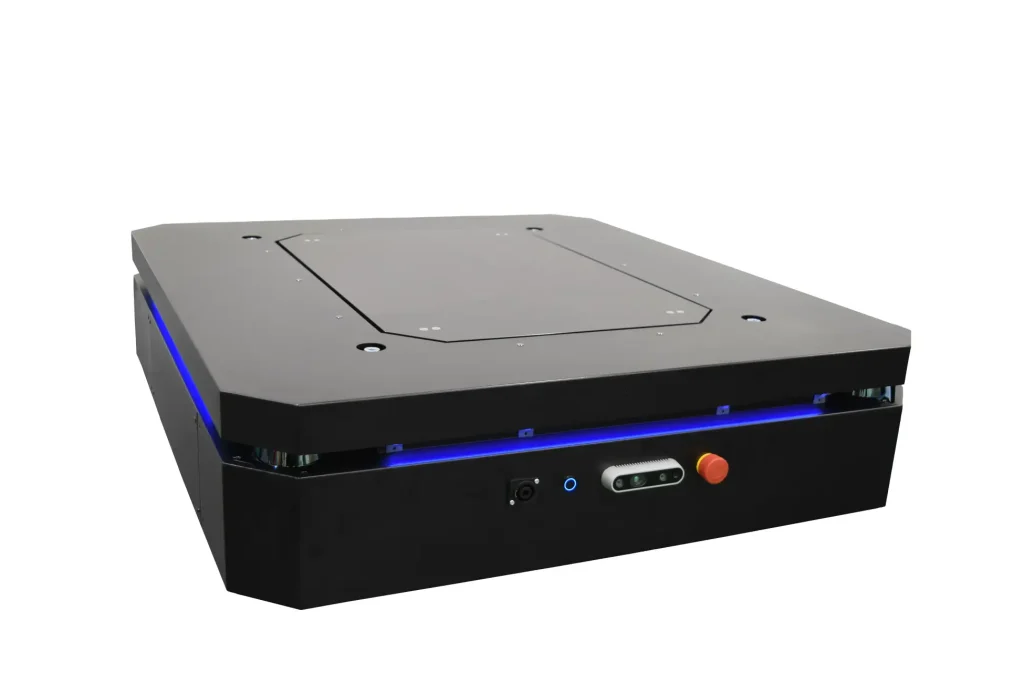
Industry Alpha 低床型 AMR「kaghelo(カゲロー)」
Challenges and prospects for AMR
While the AGVs used up until now only had to move along a guide, AMRs need to create a map of the environment in advance, understand their current location, detect obstacles, and generate a route to the destination, so software performance is extremely important.
Many of the AMRs currently in use use OSS (open source software) for their software. This has the following problems:
Difficulty in guaranteeing quality It is difficult to guarantee software quality, and it is difficult to know the appropriate way to deal with errors when they occur.
Restrictions on detailed settings For example, while it is possible to set the speed, it is not always possible to set the acceleration, and parameters that can be set sufficiently are not always provided, making it difficult to achieve detailed customization.
We have been committed to developing our own Japanese AMRs and have developed the core part of the software in-house. This time, we will use the subsidy to further strengthen this initiative and contribute to reducing the labor force in factories and warehouses, which are the foundation of Japanese manufacturing.